0 前言
金属锻造是国民经济的基础产业,在工业生产和国民经济中占有重要地位。经过多年的发展,我国已成为世界锻造生产大国。据中国锻压学会统计,2009年我国的锻件总产量达776万t,比2008年增长43%。但我国锻造产品多集中在中小型、低价值、非精密、高污染的锻件上,高端精密锻件严重依赖进口。据统计,我国每吨锻件平均消耗的能源为1.3~1.5t标准煤,而日本每吨锻件耗能仅为0.515t标准煤,只有我国的37%。因此,在我国推广精密、节能、省材的绿色锻造新技术,是重要而紧迫的任务。
1 多向模锻——绿色优良的锻造技术
多向模锻技术是一种理想的精密优质、节能省材的锻造技术,其特点是模具闭合后,几个冲头自不同方向对毛坯进行穿孔/挤压,从而在一次加热和压机一次行程中完成复杂锻件,特别是带内空腔或凹凸外形锻件的成形(图1)。
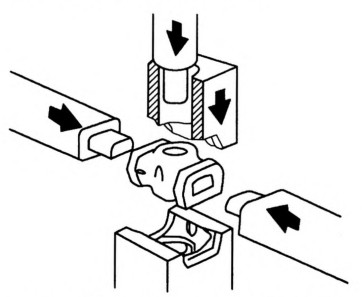
图1 多向模锻的复合分模工艺示意图
多向模锻结合了普通模锻与挤压的特点,既具有挤压工艺在巨大三向压应力下塑性变形的优点,如材料塑性提高、变形均匀、组织致密、流线完整、易于消除缺陷、制件力学性能和耐腐蚀性能好等;又具有闭式模锻的优点,如制件形状复杂、成形精度高等。同时还具有坯料形状简单、制坯成本低、复杂零件可一次成形、工序少、火次少、有效降低能耗和材料烧损的优点,是大型、高性能和高价值复杂锻件(如核电和超超临界电站高温高压阀门阀体、火箭和鱼雷壳体、导弹喷管、飞机起落架以及涡轮盘等)的理想锻造工艺。
由于多向模锻可以锻造出零件的内孔和侧向结构,所以可提高材料利用率近1倍,并减少后续切削加工约70%的工作量。仅提高材料利用率一项,每年就可以为一个年产5万t大中型多向精密锻件的生产企业,节省原材料8.3万t。若按每吨锻件耗能1.4t标准煤计算,可节省11.6万t标准煤,相当于减少C02排放22.5万t。可见,多向模锻技术是一种具有显著节能减排效果的锻造技术。
多向模锻还是一种精密、优质锻件的生产技术,是生产核电和超超临界火电阀门阀体以及航空航天领域难变形、高强度、复杂零件的关键制造技术(图2)。例如:垄断全球核电阀门市场的Velan公司,其阀门阀体的锻造就是依托Cameron公司(1997年后与Wyman.Gordon合并)的100MN、180MN和300MN等三台多向模锻液压机的制造能力。若不掌握重型多向模锻液压机及多向模锻工艺,就无法解决大规格、高等级阀门的制造技术瓶颈,就无法实现核电、超超临界核电阀门的自主化产生。
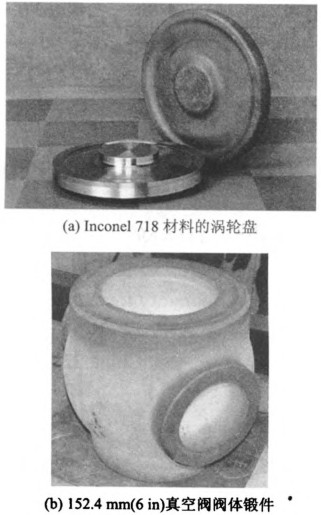
图2 多向模锻制造的精密锻件
航空航天锻件是Cameron公司最重要的锻件产品,特别是钛合金、高温合金等贵重金属锻件以及起落架、套筒、火箭喷管、涡轮盘等复杂锻件。Cameron公司利用其装备的300MN多向模锻液压机,生产的起落架锻件可节材50%,而力学性能大大提高;生产的压气机盘强度达1250~1650MPa,比标准的1200MPa高出4%~38%,而伸长率达20%,比标准的10%提高l倍。
20世纪70年代,美国空军及波音公司的对比研究证明:多向模锻制造的起落架锻件寿命可提高3~4倍,而制造成本可降低20%。因此,英美飞机起落架等筒形零件,多数是在该300MN多向模锻液压机上进行锻造的。
我国在20世纪80年代初对起落架外套进行多向模锻与普通模锻的对比研究,证明多向模锻锻件的组织致密,力学性能提高20%,而材料利用率则提高了1倍,由原来的17.3%提高到34.3%。
总之,多向模锻制造技术是一种优质、省材、低耗的绿色锻造技术,开展多向模锻制造技术的研究和推广,在促进我国锻造行业的节能、减排技术进步的同时,还能满足我国核电、超超临界火电和航空航天领域对大中型精密、高端锻件的迫切需求。
2 多向模锻液压机及其结构特点
多向模锻技术最早由美国Cameron公司于20世纪50年代提出,并建造了100MN、180MN和300MN三台多向模锻液压机,使多向模锻技术迅速投入工业生产。到20世纪60年代末,美国先后装备了36~300MN多向模锻液压机7台。德国的1台300MN液压机配置了10MN的水平侧缸。
前苏联于20世纪70年代开始研制多向模锻液压机。在进行了6.3~10MN小型多向模锻液压机的研究后,开始研制30~160MN的大型多向模锻液压机。而且在为法国建造650MN模锻液压机时,提出了配置两个70MN水平液压缸的多向模锻液压机方案。但该压机最终只完成了垂直部分。
前苏联还曾计划建造1台500MN多向模锻液压机,并且研制了5MN和37MN试验样机,对其进行了结构和液压控制方面的研究。
我国在20世纪80~90年代对多向模锻工艺及设备开展过不少研究。1971年,上重公司和西安重型机械研究所为开封高压阀门厂曾设计制造了8MN多向模锻液压机,1974年,第二重型机器厂为西南铝建造了100MN多向模锻液压机,为我国目前最大的多向模锻液压机。1980年,清华大学与第二重型机器厂合作研制了10MN多向模锻液压机样机,1996年,第一重型机器厂和燕山大学开展了“20MN多向模锻工业试验”项目。我国还开展了火箭喷管、起落架套筒、球形接头、阀门阀体等零件的多向模锻工艺的探索和研究。
2000年后,中北大学和合肥工业大学分别研制12.5MN和6.3MN多向模锻液压机,并开展了三通、履带板等典型多向模锻锻件的工艺研究。中南大学采用先进的计算机控制系统,对国内100MN多向模锻液压机的液压控制系统进行了改造。
综上,目前世界最大的多向模锻液压机为Cameron公司于1967年建造的300MN多向模锻液压机。而万吨以上的多向模锻液压机也屈指可数,美英拥有最多,有4~5台,分别属于Wyman.Gordon公司和Ellwood公司等,俄罗斯拥有1~2台,德国和中国分别拥有1台。
万吨以上、尤其是侧向水平压制力超过2千t的大型或重型多向模锻液压机是生产制造高性能大型模锻件的核心技术,也最能体现多向模锻制造节材、降耗和锻件性能优良的技术特点及产品竞争力。然而,大型或重型多向模锻的水平穿孔力或合模力,对压机机架的水平承载能力提出较高要求,使机架的设计制造困难增大。
目前,国际重型多向模锻液压机的承载机架主要采用整体机架结构和独立水平机架结构两种形式(图3)。整体机架结构(图3a)是利用一个框架同时承受垂直方向压制载荷,Fv和水平方向压制载荷Fh的结构形式。Cameron公司的180MN和300MN都采用该机架结构,其特点是结构简洁、垂直压制运动机构不受到水平压制机构或机架的影响。但在框架的立柱根部(图3a中的A、B处,立柱与上下横梁的连接处),由于垂直载荷Fv和水平载荷Fh的联合作用,此处的应力会急剧增加。而且立柱内侧根部是典型的应力集中区域,又进一步加剧了此处的强度问题,导致机架的强度要求提高。因此,采用整体机架结构的多向模锻液压机都采用性能较好的厚钢板层叠结构,而且水平载荷凡一般不大于垂直载荷Fv的1/4,即侧力比f=Fh:Fv≤1:4。以衡量多向模锻压机侧向压制能力相对主方向压制能力的大小。
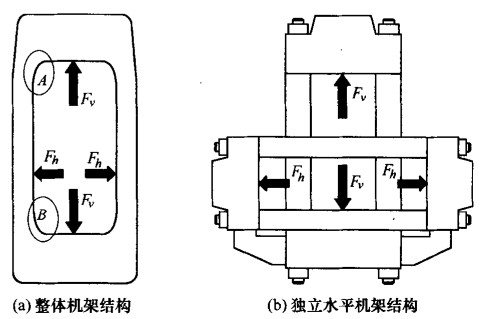
图3 多向模锻液压机的承载机架结构形式
独立水平机架结构(图3b)是在只承受垂直方向压制载荷Fv的垂直机架基础上,增加一个水平机架来独立地承受水平方向压制载荷Fh。我国和Cameron公司的100MN都采用这一结构,其特点是水平载荷与垂直载荷分别由不同结构承载,不会造成应力的叠加,水平和垂直方向的压制能力可以非常接近。但由于工作区重叠,两个机架在工作区域(即垂直压制的动梁与工作台之间)必须相互避让,水平机架的立柱需要穿过或绕过垂直机架。尤其是当压机的垂直吨位增大,垂直机架和工作台也随之加大时,水平机架的设计难度会急剧增加。若水平机架绕过垂直机架,则水平机架的结构会变得非常庞大,而且会影响到垂直压制机构的布置和维护操作:若水平机架穿过垂直机架,则会严重削弱垂直机架(包括动梁和工作台),并影响水平机架的上下对称性,使水平机架处于严重的偏心受力状态。因此,采用独立水平机架结构的多向模锻液压机的吨位较小,一般在100MN左右;但其水平载荷Fh较大,侧力比f可达l/2,即f=Fh:Fv≤1:2=0.5。
上述分析表明,重型多向模锻液压机的承载机架设计存在着受力合理性和结构合理性的矛盾。整体机架结构在垂直和水平压制结构上相互影响小,但垂直和水平压制载荷产生的应力会相互叠加。即满足了结构的独立性,但受力相互影响;独立水平机架结构则是垂直和水平压制载荷互不影响,但垂直和水平压制结构相互干涉、影响,即满足了受力的独立性,但结构相互干涉。
因此,重型多向模锻液压机机架设计的核心矛盾是受力和结构的独立性不能同时满足,即受力独立性与结构独立性间存在冲突。而目前的多向模锻液压机机架结构都不能很好地解决这一核心矛盾,因此当今多向模锻液压机的最大吨位只达到300MN,而最大的水平压制能力只达到60MN。这一由重型多向模锻液压机功能特点导致的结构设计矛盾,制约了多向模锻制造技术的进一步发展。
3 多向承载结构设计的突破
在教育部985II期重点项目——多功能金属成形试验平台的实施过程中,为了克服多向承载结构的设计难题,基于预应力钢丝缠绕技术,提出了“正交预紧机架”结构,即利用高强度预应力钢丝缠绕在多段圆弧和直线组成的整体机架外轮廓上,产生与多向压制载荷方向对应的预紧力,平衡多向载荷产生的应力,进而消除应力叠加对机架的不利影响和强度要求。
普通预应力钢丝缠绕机架如图4a所示。机架由上下半圆梁和两根立柱组成,构成由上下两段180°圆弧和两段直线组成的机架轮廓。预应力钢丝缠绕在机架外轮廓上,在圆弧段钢丝改变方向,对弧面产生压力,并随缠绕层的增多,压力逐渐增大。而圆弧上压力的合力就是钢丝缠绕产生的预紧力Pv。对于普通预应力钢丝缠绕机架,其机架轮廓的圆弧集中在上下两端,因此钢丝缠绕的预紧力Pv也就集中在上下两个位置,与机架所承受的压制力重合,一般沿垂直方向。这是预应力钢丝缠绕压机机架的典型结构,已大量应用于重型模锻压机、挤压机等重型液压机上。
在普通预应力钢丝缠绕机架的基础上,可以将机架轮廓的圆弧分成4段,分别置于压机结构的上下和两侧,圆弧之间则用立柱的直线连接(图4b)。由于缠绕的钢丝在直线段不会产生预紧力,因此如图4b所示的机架轮廓可以将预应力钢丝缠绕产生的预紧力集中到上下和左右4个位置,构成垂直和水平两个正交方向的预紧力(Pv和Ph),与多向模锻需要的垂直和水平压制力(Fv和Fh)重合(图5),并平衡压制载荷对机架的影响。
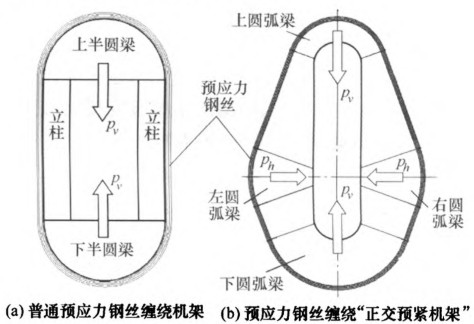
图4 普通钢丝缠绕机架与“正交预紧机架”比较
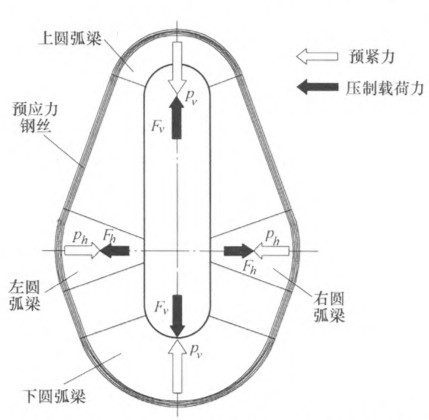
图5 预应力钢丝缠绕“正交预紧机架”的受力
由于预应力钢丝缠绕技术的特点,正交预紧机架在垂直和水平方向上产生的预紧力能够分别达到多向模锻在垂直和水平方向上最大压制吨位的1.2~2.0倍,甚至更高,可以有效地保证整体机架在承受多向载荷单独或联合作用时的安全性。因此即使是在多向压制载荷引起应力叠加的区域,钢丝缠绕产生的预应力也足够大,不会出现拉应力。
由于有效克服了整体机架多向载荷相互影响、危险应力相互叠加的问题,同时预紧力的施加没有产生新的结构干涉或强度要求,因此可以说预应力钢丝缠绕正交预紧方案很好地解决了重型多向模锻液压机机架设计的核心矛盾,为多向模锻液压机设计提供了新的结构形式。
利用这一新型结构,设计了1台40MN/64MN多向模锻液压机,其垂直最大压制吨位为40MN,水平最大压制吨位为2X8MN(侧力f=0.2),下穿孔最大吨位为8MN,四个方向总共64MN压制能力。在清华大学和中国二十二冶集团有限公司的共同努力下,该压机于2010年7月31日热试成功(图6)。随后进行的多向压制试验表明,正交预紧机架有效地承受了垂直和水平压制载荷的作用,保持了良好的整体性和承载能力。
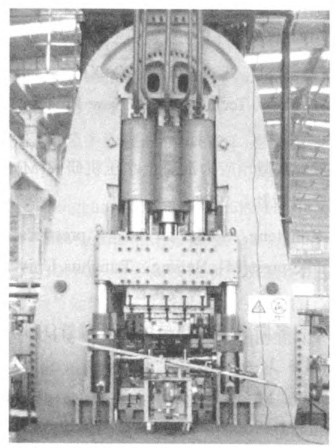
图6 应用“正交预紧机架”设计制造的40MN/64MN多向模锻液压机
在40MN/64MN多向模锻液压机上,先后试压了76.2mm(3in)阀门阀体(图7)和152.4mm(6in)真空阀阀体(图2b)。一火成形的阀体锻件充型饱满、致密,尺寸精确。40MN/64MN多向模锻液压机的研制及工艺试验,实践了预应力钢丝缠绕正交预紧机架的设计、加工、缠绕以及安装调试的整个制造过程,充分证明了该结构在更大吨位多向模锻液压机上应用的可行性。
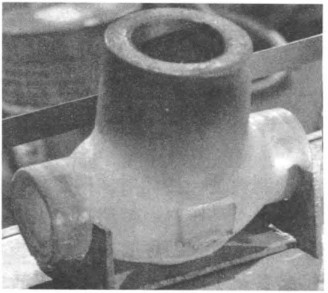
图7 在40MN/64MN多向模锻液压机上一次成形的20钢76.2mm(3in)阀体
4 发展我国重型多向模锻制造技术
2010年9月11日,由中冶集团、中国二十二冶集团有限公司和清华大学在唐山召开了“大型多向模锻设备及工艺研讨会”。国内二十多位领导、院士、专家出席并参观了40MN/64MN多向模锻液压机及76.2mm(3in)阀体的锻造演示。专家一致认为:“正交预紧机架”结构有效地解决了多向模锻液压机水平压制力承载结构设计的难题,为发展我国的多向模锻制造技术奠定了独立自主的技术基础;这是一个填补国内空白的技术突破,希望利用该项新技术,早日实现核电阀门以及航空航天等复杂精密锻件的自主化、产业化生产,为振兴民族工业做出贡献。
为此,中国二十二冶集团有限公司和清华大学合作,开展了120MN和400MN多向模锻液压机的研究和设计工作,为建立我国重型多向模锻生产基地做准备。
120MN多向模锻液压机的机架设计充分利用了正交预紧机架的结构优势,其水平压制设计吨位将达到70MN,侧力比f=l:1.71≈0.58,皆为目前世界最大值。强大的水平压制能力,将使此台压机具有强大的垂直分模成形能力。建成后将实现不大于300mm(12in)口径以下的阀体以及套筒等复杂零件的多向锻造生产。该压机的设计、制造,以及配套的模具、工艺研究已获得2012年“高端数控机床及基础装备”重大专项共性技术项目支持。
400MN多向模锻液压机将是世界最大的多向模锻液压机,其垂直最大合模力达400MN,水平最大合模力达100MN,侧力比f=0.25。生产的产品对象是300~600mm(12~24in)阀体和大型精密复杂模锻件。建成后将彻底改变多向模锻生产的世界格局,打破美英公司在重型多向模锻装备及相关产品生产上的垄断地位,建立我国在此领域的自主化生产能力,并促进我国锻造行业绿色制造技术水平的提高。
5 结论
多向模锻制造是一种优质、精密、省材、降耗的先进锻造技术,是核电、超超临界火电、石化,以及航空航天精密复杂锻件的理想成形技术。但重型多向模锻装备及生产工艺的技术难度较大,目前只有美英两国的个别公司所掌握。
正交预紧机架结构设计,通过无贯穿件的多向预紧手段,提高了整体机架承受多向载荷的能力,并且避免了水平压制结构对垂直压制结构的影响。新型机架结构突破了多向模锻液压机结构设计的核心矛盾,为开发我国自主知识产权的重型多向模锻装备,打破国际垄断,在我国推广多向模锻制造技术,奠定了装备设计的技术基础。
通过多向模锻制造技术发展和应用,将提高我国航空航天、核电、火电、石化等关键领域的基础制造能力和技术水平,实现核心零部件的自主化生产。同时还将极大地促进传统行业的技术提升,并取得显著的节能减排效果。